لاتکس
به طور کلی دیسپرسیون رزین در پروسه ی ساخت رنگ ، از نظر صرف زمان و انرژی ، پردردسر ترین مرحله می باشد . که این بواسطه ی تفاوت در تنش سطحی فاز مایع ( رزین ها و حلال ها) و فازجامد ( پیگمنت ها و فیلر ها) می باشد .
دیسپرسیون یک پلیمر به عوامل زیر وابسته می باشد:
• وزن مولکولی
• توزیع وزن مولکولی
• اندازه ذرات و نحوه توزیع آنها
• واحد های مونومری
• درجه کراس لینک شدن است
این پروسه شامل چهار مرحله است:
1. خیس شدن: جایگزینی هوا و آب با رزین
2. دانه بندی و اسیاب: شکسته شدن مکانیکی و جدا شدن ذرات و رسیدن به اندازه ی اولیه
3. دیسپرسیون: توزیع این ذرات در محمل مایع
4. پایداری: جدا ماندن ذرات برای مدت طولانی
لاتکس چیست؟
لاتکس پراکنه کلوئیدی ذرات پایدار شده به کمک ماده فعال سطحی در آّ است. فیلم های لاتکسی در اثر وجود چهار نوع تنش عمده هیدرودینامیکی، موئینگی کشسان، موئینگی و جمع شدگی پس از طی سه مرحله تغلیظ، هجوم هوا و تغییر شکل موئینگی تشکیل می شوند. در تشکیل فیلم از لاتکس پلیمری، سرعت تبخیر بستر تاثیر چشمگیری بر یکپارچگی و مشخصات نهایی فیلم دارد. به طوری که با افزایش سرعت تبخیربستر، یکپارچگی فیلم نهایی کاهش می یابد. در این سامانه ها ماده فعال سطحی با وجود تاثیر مثبت در پایداری ذرات کلوئیدیو جلوگیری از تجمع خود به خودی آنها، ضخامت فیلم را در لبه ها افزایش می دهد. چالش دیگر در تشکیل فیلم های لاتکسی اندازه و شکل هندسی فیلم است. به طوری که سرعت خشک شدن در هندسه دایره ای از لبه دایره به سمت مرکز در نقاط مختلف واقع بر محیط، یکسان و در هندسه مستطیلی در راستای دو ضلع، متفاوت است. چالش دیگر تشکیل فیلم لاتکسی، ایجاد طرح های همرفتی سطحی در اثر مصرف گرمای نهان تبخیر بستر در فصل مشترک مایع-هوا و ایجاد اختلاف دما یا غلظت از کف به سطح است.
مراحل تشکیل فیلم لاتکس
تبخیر
تغییر فرم
نفوذ در یکدیگر و انعقاد
قابلیت نفوذ در یکدیگر بستگی به Tgیا همان دمای انتقال شیشه ای رزین دارد و اگر زیر Tg باشیم تقریبا نفوذ رخ نمی دهد که که در مورد رزینهای اکریلیک پایه آب در کمتر از دمای انتقال شیشه ای آب تبخیر نمیشود و فیلم سفید می ماند.
تشکیل فیلم نیز تابع عوامل زیر است:
- دمای انتقال شیشه ای Tg
- حداقل دمای تشکیل فیلم MFFT
- عامل منعقد کننده
تا به حال تجربه داشته اید که سطل یا شیء پلاستیکی در زمستان در مجاورت هوای بیرون، نسبت به فصل تابستان، بسیار راحت تر ترک می خورد و میشکند؟ این تجربه ی شما، پدیدهای است که به نام انتقال شیشهای شناخته میشود. این انتقال، پدیده ای خاص پلیمرها ست و یکی از خواصی است که پلیمرها را منحصر به فرد می کند. انتقال شیشه ای بسیار مهم تر از آن چیزی است که به نظر می رسد. برای هر پلیمر دمای خاص و منحصر به فردی وجود دارد که دمای انتقال شیشهای، یا به اختصار Tg نامیده میشود. وقتی پلیمر تا دماهای زیر Tg خود سرد شود، مثل شیشه، سخت و شکننده میشود. بعضی پلیمرها در بالای Tg خود، و برخی دیگر در زیر Tg استفاده میشوند. پلاستیکهای سخت مانند پلیاستایرن و پلی(متیل متاکریلات) در دماهای زیر Tg ، به عبارتی در حالت شیشه ای کاربرد دارند. آنها کاملاً بالاتر از دمای اتاق، و برای هردو در حدود C° ۱۰۰ است .الاستومرهای لاستیکی مثل پلیایزوپرن و پلیایزوبوتیلن، در دمای بالای Tg خود ، در حالت لاستیکی، استفاده میشوند، که در آن انعطافپذیر و نرم میباشند.
هر چه MFFT پایین تر باشد تشکیل فیلم راحت تر است. به همین منظور جهت کم کردن حداقل دمای تشکیل فیلم روشهایی در نظر گرفته شده است که در ادامه به طور خلاصه به آنها پرداخته میشود:
استفاده از تکنولوژی هسته- پوسته( Core-shell )
در این روش معمولا رزین سنتز شده حاوی یک پوسته نرم (برای نفوذ) و هسته سخت (برای افزایش مقاومت مکانیکی) است..
استفاده از عامل انعقاد
عامل انعقاد به طور موقت ذرات پلیمری را نرم میکند و بعد از سیستم خارج می شود و ماهیت پلیمر مثل قبل می شود. در ضمن باید از حلالی استفاده شود که نقطه تبخیرش بیشتر از آب باشد چرا که اگر زودتر از آب از سیستم خارج شود تاثیری در روند تشکیل فیلم ندارد.
مثالی برای عامل انعقاد:
گلایکول ها: گلایکول ها زمان باز شدگی را افزایش می دهند که باعث براقیت بالا و قلم خوری خوب می شوند.
بهترین و موثرترین عوامل وایت اسپریت است.
اثرات عامل انعقاد:
پایین آوردنMFFT که باعث می شود تشکیل فیلم در دمای پایین تری رخ دهد.
بالا بردن میزان نفوذ به دلیل افزایش تورم ذرات.
عوامل تر کننده (wetting agent)
تر شدن به حالتی گفته میشود که هوای بین پیگمنت ها با حلال جایگزین شود. تر شدن پیگمنت ها به کشش سطحی دو فاز بستگی دارد. هر چه کشش سطحی دو فاز به هم نزدیک تر باشد تر شدن بهتر اتفاق می افتد.
آب حلالی با انرژی سطحی بالاست و تمایلی به تر کردن پودر ها ندارد. یک راه برای پایین آوردن کشش سطحی، استفاده از پروپیلن گلایکول و دیگری استفاده از عوامل ترکننده مثل هگزا متا فسفات است.
دیسپرس کردن معمولا با همزن انجام می شود و در این مرحله ویسکوزیته بسیار مهم است, چون اگر ویسکوزیته خیلی بالا باشد دما خیلی بالا می رود و باعث می شود مواد اضافه شده تبخیر شوند و اگر ویسکوزیته خیلی پایین هم باشد ذرات با هم تماس پیدا نمی کنند و برخورد ندارند.
در مطالب بعدی راجع به بقیه مواد تشکیل دهنده رنگ ها و عایق های رطوبتی پلیمری پایه آب توضیح خواهیم داد.
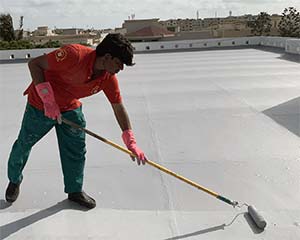
نانوشیلد محصولات متنوعی از عایقهای رطوبتی کاربردهای گوناگون را در اختیار مشتریان خود قرار میدهد و تقریبا تمامی این محصولات را میتوانید با استفاده از قلم مو، غلطک و ایرلس اجرا کنید. در ادامه با توضیحات تکمیلی در رابطه به چگونگی اجرای عایق رطوبتی نانوشیلد بیشتر آشنا خواهید شد
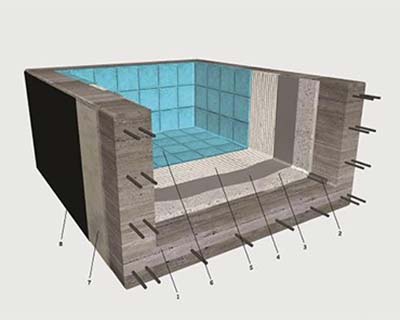
عایق رطوبتی فشار منفی به نوعی از عایق رطوبتی گفته میشود که برای محافظت از سازهها در برابر نفوذ آب از سطح خارجی به سطح داخلی در سازه اعمال و اجرا میشود. به بیان سادهتر، این نوع عایق زمانی بکار میرود که احتمال نفوذ آب و رطوبت از خارج به داخل سازه وجود دارد.
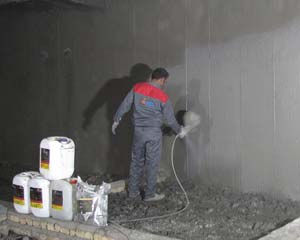
یکی از پرسشهای اساسی در رابطه با عایق کاری و آب بندی این است که چقدر باید صبر کنیم تا عایق رطوبتی نانو خشک شود؟ دانستن پاسخ این سوال نقش بسیار مهمی در کیفیت عایق کاری و آب بندی سطوح دارد. پاسخ کوتاه این است: حداکثر 72 ساعت اما اگر میخواهید پاسخ دقیق را بدانید با ادامه این یادداشت همراه شوید
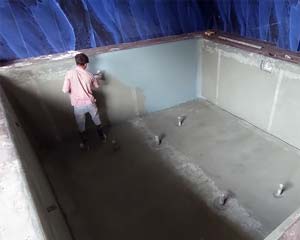
عایقهای نانو کاربردهای وسیعی دارد و برای آب بندی سطوح مختلفی از جمله سطوح فلزی و چوبی و همچنین به عنوان یک لایه ضد اب و رطوبت بر روی انواع مصالح ساختمانی استفاده میشود. در این مطلب به نحوه استفاده از عایق نانو میپردازیم.
جستجو
سبد خرید